Packaging Machine Repair Service: Guaranteeing Marginal Downtime and Optimum Performance
Packaging Machine Repair Service: Guaranteeing Marginal Downtime and Optimum Performance
Blog Article
Understanding the Key Parts and Repair Approaches for Packaging Equipment Maintenance
Reliable maintenance of product packaging devices depends upon a thorough understanding of their crucial components, including the structure, drive system, and securing systems. Recognizing common upkeep problems, paired with the execution of preventative techniques and repairing strategies, can significantly enhance machine reliability. The selection of repair service practices, including the use of OEM parts and the importance of licensed specialists, plays an important duty in reducing downtime. To absolutely comprehend the details of these systems and their maintenance, one need to take into consideration the broader effects of neglecting these important methods.
Key Parts of Packaging Machines
Packaging makers include several vital components that interact to ensure effective and reliable product packaging processes. At the core of these devices is the framework, which offers architectural integrity and houses the numerous operating components. The drive system, commonly a mix of electric motors and equipments, facilitates the activity of elements, making it possible for exact operation throughout the product packaging cycle.
An additional important part is the conveyor system, which moves items via different stages of the packaging process. This is typically enhanced by sensors and controls that keep track of the position and rate of products, guaranteeing synchronization and minimizing mistakes. The filling system is vital for accurately dispensing the appropriate quantity of item right into plans, whether in liquid, powder, or solid form.
Securing mechanisms, consisting of warmth sealants or sticky applicators, play a crucial function in safeguarding plans, preventing contamination and prolonging service life. Furthermore, classifying systems are indispensable for providing needed item information, ensuring conformity with regulations. Ultimately, the control panel, furnished with straightforward interfaces, permits drivers to handle equipment features, monitor performance, and make adjustments as required, ensuring optimum efficiency and performance in product packaging procedures.
Common Maintenance Concerns
Reliable operation of product packaging equipments depends greatly on regular upkeep to stop usual problems that can interrupt production. Among these problems, mechanical wear and tear prevails, particularly in elements like conveyors, motors, and seals, which can bring about unforeseen downtimes. Additionally, misalignment of components can result in inefficient procedure, causing items to be improperly packaged or damaged throughout the procedure.
An additional usual maintenance issue involves the accumulation of dirt and particles, which can disrupt the machine's sensing units and moving components. packaging machine repair service. This not only affects performance however can likewise present safety and security risks. Lubrication failings can lead to boosted friction, resulting in getting too hot and eventual component failure.
Electrical issues, usually originating from loosened links or worn-out electrical wiring, can interrupt machinery functions, leading to substantial manufacturing hold-ups. Finally, software application glitches due to outdated programs or inappropriate arrangements can prevent the maker's operation, necessitating instant intervention. Dealing with these usual upkeep issues proactively is essential for making sure optimal efficiency and durability of product packaging equipment.
Preventative Maintenance Approaches
Executing preventative upkeep methods is crucial for maintaining the efficiency and integrity of packaging equipments. These methods encompass an organized method to upkeep, concentrating on the routine inspection and maintenance of equipment to preempt prospective failures. By adhering to a set up maintenance program, operators can determine deterioration on components prior to they bring about considerable failures.
Crucial element of a preventative maintenance technique consist of regular evaluations, cleaning, element, and lubrication replacements based on maker referrals. Utilizing checklists can enhance this procedure, making certain that no necessary tasks are forgotten. Additionally, preserving exact records of maintenance activities help in tracking the equipment's efficiency over time, helping with educated decision-making regarding future maintenance needs.
Training staff on the significance of preventative upkeep enhances conformity and cultivates a culture of proactive care. Applying an anticipating maintenance element, using data analytics and sensing unit modern technology, can even more enhance equipment explanation performance by anticipating failures before they occur.
Fixing Methods
When faced with breakdowns or inadequacies in product packaging makers, utilizing systematic troubleshooting strategies is necessary for determining and dealing with problems swiftly. The initial action in effective troubleshooting is to develop a clear understanding of the equipment's operational parameters and efficiency metrics. This involves assessing the maker's requirements, along with any type of mistake signals or codes displayed.
Following, operators need to carry out a visual assessment, looking for noticeable indicators of misalignment, damages, or wear. This often consists of examining sensors, belts, and gears to determine potential reasons for malfunction. Collecting operational information, such as manufacturing rates and downtime logs, can likewise give insights right into repeating problems.
As soon as potential issues are identified, making use of a logical technique to separate the root cause is vital. This might require screening specific components or systems in a controlled way. Taking part in conversations anchor with operators who engage with the equipment routinely can produce useful responses about unusual habits or patterns.
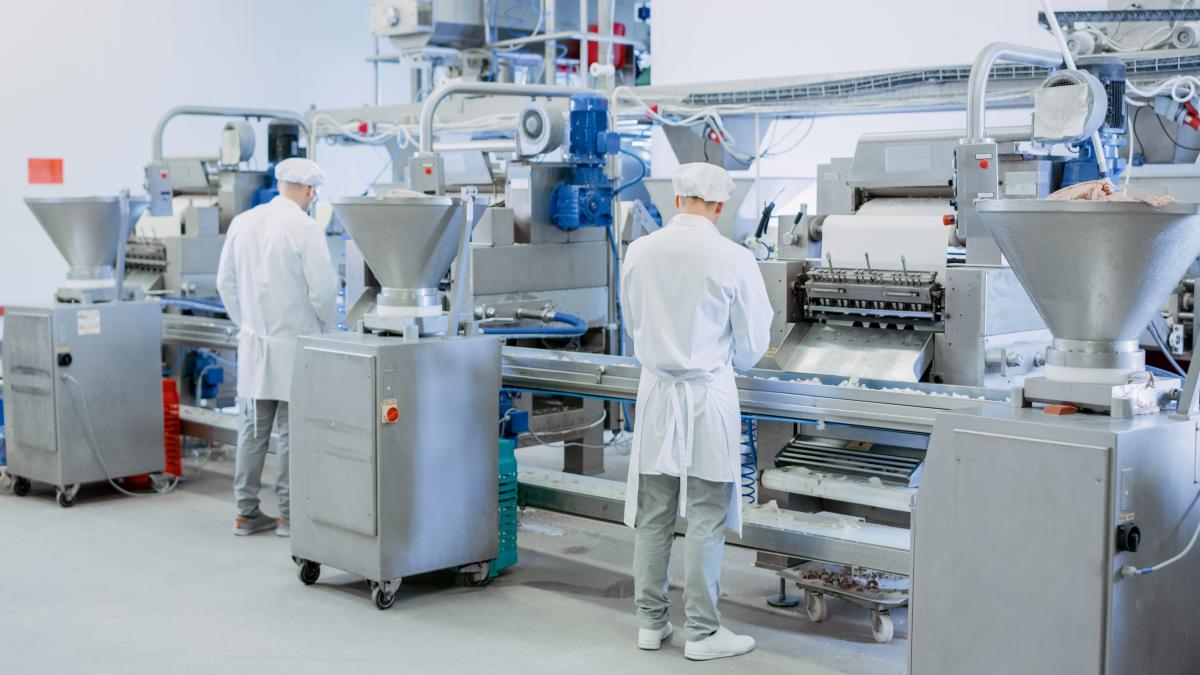
Repair and Substitute Ideal Practices
A thorough understanding of repair service and replacement best techniques is essential for preserving the longevity and efficiency of product packaging equipments. On a regular basis evaluating the condition of equipment elements enables prompt intervention, preventing even more considerable issues that can cause expensive downtimes.
When repair work are essential, it is necessary to utilize OEM (Original Tools Maker) parts to make sure compatibility and performance. This not just preserves the stability of the machine yet also maintains warranty arrangements. Additionally, it is suggested to maintain a stock of crucial extra parts to facilitate quick substitutes and reduce functional disturbances.
For complicated fixings, engaging certified technicians with specialized training in product packaging machinery is advised. They have the competence to diagnose issues precisely and perform fixings effectively. Additionally, documenting all fixing tasks and parts substitutes is critical for maintaining a detailed upkeep background, which can aid in future troubleshooting.
Finally, executing a proactive approach, consisting of routine evaluations and anticipating upkeep strategies, improves the dependability of product packaging equipments. By sticking to these ideal techniques, businesses can ensure optimal device performance, reduce operational risks, and expand tools life expectancy.
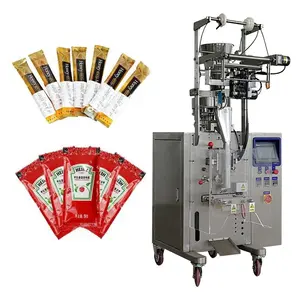
Verdict
Finally, a detailed understanding of product packaging maker components and Discover More reliable maintenance approaches is important for optimum performance. Normal inspections and the usage of OEM parts can dramatically reduce downtime, while a well-documented upkeep history cultivates proactive care. Utilizing certified service technicians further improves repair high quality and integrity. By implementing these methods, companies can guarantee the durability and performance of packaging makers, inevitably adding to enhanced functional performance and reduced expenses.
Efficient maintenance of packaging devices hinges on a detailed understanding of their key parts, consisting of the frame, drive system, and sealing systems.Efficient procedure of packaging makers depends greatly on routine maintenance to avoid typical problems that can interrupt production.Executing preventative maintenance methods is crucial for maintaining the performance and integrity of product packaging makers. Furthermore, preserving accurate records of maintenance activities help in tracking the maker's efficiency over time, helping with notified decision-making regarding future maintenance needs.
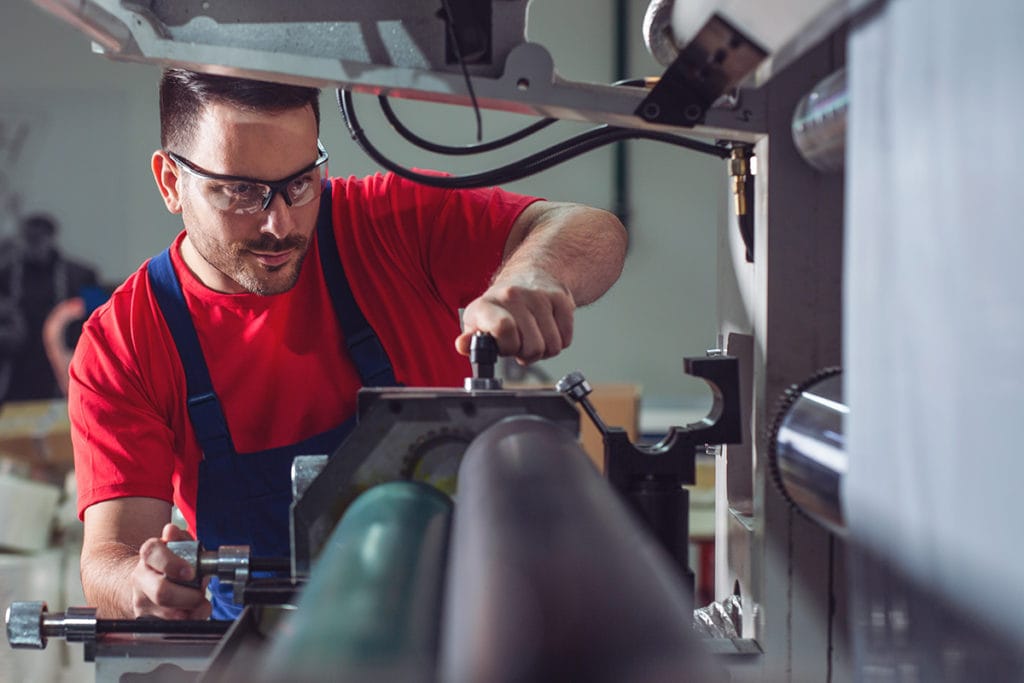
Report this page